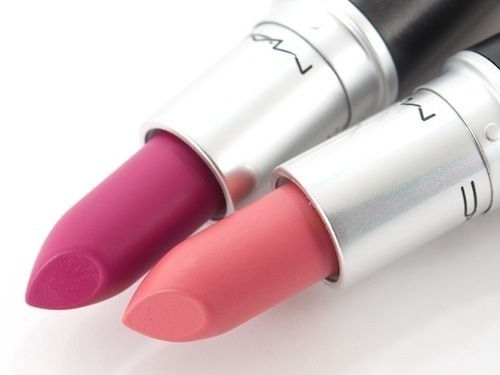


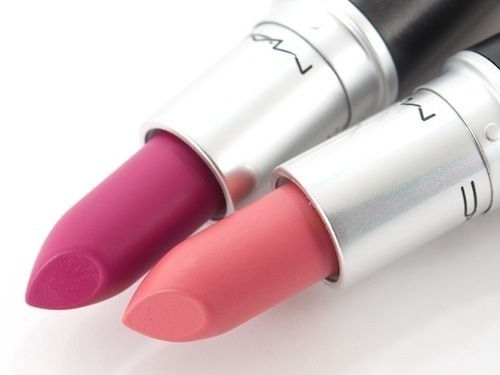
Le rouge à lèvres

Beaucoup de femmes dépensent énormément pour leurs rouge à lèvres, d'autres moins... Mais savent-elle comment il est fabriqué?
Bien qu’il existe des règles basiques de formulation et de fabrication, tout l’art du formulateur consiste à jouer avec les ratios classiquement connus afin d’apporter au produit fini des caractéristiques variables tout en restant dans des critères d’acceptation qualité. Les méthodes, les machines ont beaucoup évoluées. Leurs techniques sont bien meilleures que la nôtre bien évidemment...
Nous avons tenté de visiter une usine de fabrication chez de grandes enseignes tel que Dior, l'Oréal, Lancôme mais malheureusement, notre demande n'a pas été acceptée due au secret professionel. Mais nous avons tant bien que mal réussi à répondre à notre question..
Pour commencer, voici les différentes étapes de fabrication:
Fabrication industrielle

Intéressons nous au broyage des pigments:
Le broyage des pigments est une étape fondamentale à la fabrication. En effet, il faut faire un sorte que le résultat obtenu soit le plus fin possible, afin d’avoir un résultat final meilleur. Elle est déterminante de la texture comme pour l’aspect du bâton.
Comme nous l’avons exécuté lors de la fabrication de notre propre rouge à lèvres, il est possible de mélanger les pigments avec l'huile et d’écraser ce mélange. Mais bien évidemment cette technique est loin d’être la plus parfaite car les pigments ne seront pas très fins au final.
Le dernier « chef d’œuvre des ingénieurs » est le broyeur à bille.
Le principe du broyeur à bille
Le schéma ci-contre est une représentation simplifiée du principe rotor/stator.
Le stator est immobile, de forme cylindrique ou cônique. Le rotor lui, est en rotation grâce à son arbre de rotation
Lorsque l’on applique une tension électrique sur le stator, il y a un champ magnétique (principe aimant) qui se créer dans l’entre fer, ce qui fait tourner le rotor. Plus le champ magnétique est grand, plus la vitesse augmente.
Lorsque le rotor tourne, les billes placées à l’intérieur sont projetées vers l’extérieur jusqu’à cogner la paroi avec une accélération qui enduit une énergie cinétique (= ½ m.v²). L’énergie cinétique est proportionnelle à la force de cisaillement. C’est cette force qui permet de broyer les pigments. Il faut que la force de cisaillement soit suffisante pour que les molécules des pigments soient broyées.
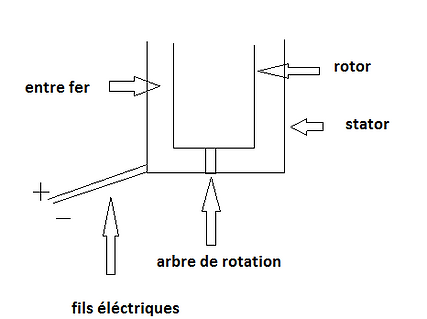
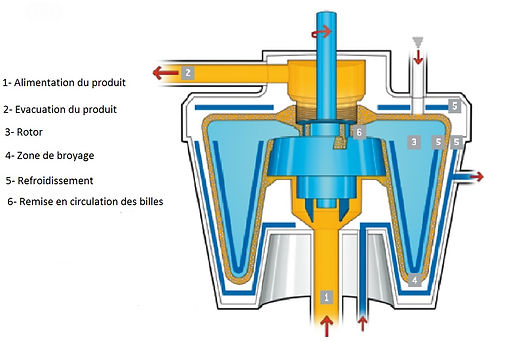
Les pigments sont ajoutés avec les billes par le billet d’une pompe à puissance dans la chambre de travail, le rotor (1). Ensuite les pigments broyés sont sortis à l’aide de la pompe (2).
Il faut ensuite mélanger les cires avec les huiles afin d’obtenir une base blanche dans une fonte en cuve. Ensuite agitation sous turbine et coulage en pain. (image ci-contre).

Après ces premières étapes, viens ensuite le mélange des deux produits obtenus en turbine en ajoutant les nacres.
Voilà ce que l’on obtient après la deuxième étape (image ci-contre). Cette forme compactée du rouge à lèvres va être ensuite coupée en morceau et insérer dans une autre machine une cuve chauffante, qui permettra de faire fondre pour ensuite pouvoir la mettre en œuvre pour obtenir le bâton finale. La cuve est chauffée à environ 90° (image ci-dessous).

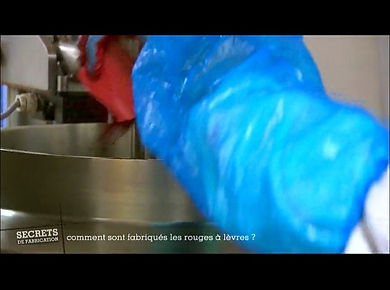

Après la fonte de la base, celle-ci est entrainée par des tuyaux et va être écoulée dans des moules métalliques avec une quantité précise.
La machine fait ensuite refroidir le contenu de chaque moule. Les bâtons sont ensuite insérés dans leur tube.
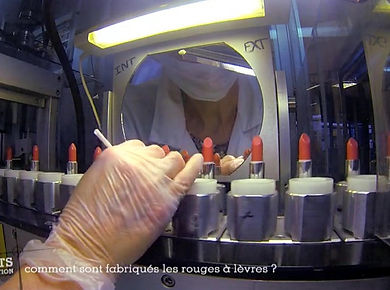
Les bâtons solidifiés sont par la suite récupérés pour une étape très importante, le contrôle visuel. Cette étape consiste à contrôler visuellement un à un les produits pour vérifier le moindre défaut de fabrication. Cela nécessite de l'expérience. Le rouge à lèvres peut être par exemple pas tout à fait lisse, il sera donc retiré de la chaine.
Ci-dessous est représenté le véritable schéma du broyeur à billes.
Schéma de la fabrication industrielle du rouge à lèvre
Schéma explicatif du principe rotor/stator
© Created By Mrs Bhatti, Mrs Zouagha and Mrs Sripaskar
October 2013 - February 2014